Gravity Energy Storage Systems with Weight Lifting
Principle of Operation
Gravity energy storage (GES) is an innovative technology to store electricity as the potential energy of solid weights lifted against the Earth's gravity force. When surplus electricity is available, it is used to lift weights. When electricity demand is high, the weights descend by the force of gravity and potential energy converts back into electricity (Fig. 1). A specific GES configuration that uses pulley systems working in tandem with a motor-generator to move the weights is known as lifted weight storage (LWS).
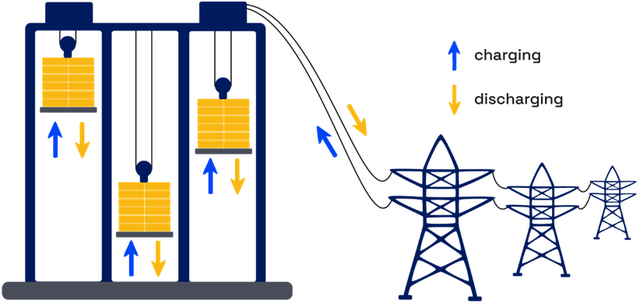
Figure 1. Schematic of LWS. Source: www.gravient.com.
Technical Characteristics
The energy capacity of LWS is proportional to the cumulative potential energy of weights
\[E=M g H,\]
|
(1) |
where \(M\) is the total mass of all the weights, \(g\) is the acceleration due to gravity, and \(H\) is the height of vertical movement of the gravity center of the weights (Berrada, Loudiyi, and Zorkani, 2017; Franklin, et al., 2022; Morstyn and Botha, 2022; Li et al., 2023). The installed power of LWS is equal to the sum of operating power of all incorporated lifting systems (Kropotin and Marchuk, 2023a). The LWS efficiency depends on the efficiency of the lifting mechanisms. It has been shown that the round-trip efficiency of the LWS can reach 86% (Kropotin and Marchuk, 2023b).
The operational principle of LWS eliminates the fire hazards of lithium-ion batteries and flooding risks specific to pumped-hydro storage (PHS). LWS is virtually free from disadvantages, such as degradation of performance over time or the cycle number limit. The former is due to the absence of leakage currents in the given engineering solution, as occurs in Li-ion batteries, and loss of weight mass, as occurs in PHS. The latter is related to the fact that the number of charge–discharge cycles weakly affects the lifetime of the structure and the equipment degradation is eliminated by repairs, which are classified as operations and maintenance costs (O&M).
The structure with a height of more than 100 meters has an area comparable to that of a Li-ion storage system of the same power and energy capacity (Kropotin, Penkov, and Marchuk, 2023). The majority of the literature on GES highlights its extended service life of about 40–60 years (Berrada, Loudiyi, and Zorkani, 2016; Berrada, 2022), high full-cycle efficiency of about 85% (Emrani et al., 2022; Kropotin and Marchuk, 2023b), and even the high maneuverability in the range of milliseconds (Tong et al., 2023). Thus, LWS can provide: load shifting, renewable energy integration, black start capability, absorbance of reactive power, and even fast-response frequency regulation.
Economic Characteristics
From a technical point of view, LWS is capable of providing at least the same services as Li-ion batteries. Therefore, the revenue stream for LWS is no less than that of Li-ion storage and the main question lies in the comparison of expenses. The total capital expenditures [\$] of LWS depend on the energy capacity \(E\) [MWh] and installed power \(P\) [MW] (Kropotin and Marchuk, 2023a):
\[\text{CAPEX}=\left(\dfrac{p_w}{\alpha_M}+\dfrac{p_s}{\alpha_V}+\dfrac{p_f+p_r}{\alpha_S}\right)E+p_hP+\dfrac{p_{ew}}{\alpha_{Sew}/k}\sqrt{E},\]
|
(2) |
where \(p_w\), \(p_s\), \(p_f\), \(p_r\), \(p_h\), and \(p_{ew}\) are the prices of weights [\$/ton], bearing skeleton [\$/m3], foundation [\$/m\({}^{2}\)], roof [\$/m2], hoist [\$/MW], and external walls [\$/m2], respectively; \(\alpha_M\), \(\alpha_V\), \(\alpha_S\), \(\alpha_{Sew}\), and \(k\) are the constants which depends on the geometry of the bearing skeleton and the weights. Equation (2) implies that the capital expenditures by a unit of energy capacity (\(\text{capex} = \text{CAPEX}/E\)) fall with increasing energy capacity \(E\), regardless of the fall in prices \(p_i\) that occur due to economies of scale:
\[\text{capex}=\left(\dfrac{p_w}{\alpha_M}+\dfrac{p_s}{\alpha_V}+\dfrac{p_f+p_r}{\alpha_S}\right)+p_h\dfrac{P}{E}+{\left(\dfrac{p_{ew}}{{\alpha_{Sew}}/{k}}\right)}\Big/\!\sqrt{E}\xrightarrow[E\to\infty]{}\dfrac{p_w}{\alpha_M}+\dfrac{p_s}{\alpha_V}+\dfrac{p_f+p_r}{\alpha_S}.\]
|
(3) |
This means that, unlike other energy storage technologies, the capex of the gravity storage system decreases as it scales up, not only due to economies of scale but also due to the design of the LWS itself. Thus, as the LWS capacity increases, we have a double effect of capex drops.
A quantitative assessment without taking into account economies of scale showed that the capex can be reduced to nearly 450 \$/kWh (Kropotin and Marchuk, 2023a). The value was calculated using the prices \(p_i\) that includes the costs of materials, labor, taxes, equipment, subcontractors, overheads as well as construction company profits. Due to the design simplicity, annual O&M costs are quite accurately estimated based on the datasheets of widely used devices and materials of the LWS and accounted for less than 0.5% of CAPEX (Berrada, Loudiyi, and Zorkani, 2016; Berrada, 2022). To summarize the costs and facilitate an economic comparing of an LWS with a Li-ion one, the total cost of ownership has to be calculated as follows:
\[\text{TCO}=\text{CAPEX}(2-\text{DoD})\left[1+\text{O&M}\left(N_\text{years}-1\right)+\text{RC}\cdot {\rm div}\left(\frac{N_\text{years}-1}{\text{LT}}\right)\right],\]
|
(4) |
where CAPEX represents capital expenditures, DoD is the depth of discharge, O&M is the annual operations and maintenance cost [% of CAPEX], RC is the reconstruction cost, LT is the storage system lifetime [years], \(N_\text{years}\) is the ownership period [years], and \({\rm div}\) is the function calculates the floor integer part of division.
Results of calculations based on Eq. (4) are shown in Fig. 2. Data from the U.S. Department of Energy report by Viswanathan et al. (2022) are used as the input for the Li-ion battery case, while the data for LWS is sourced from Kropotin and Marchuk (2023a). It follows from Fig. 2 that the benefit of using LWS as compared to that for the Li-ion batteries becomes substantial from the moment of the first Li-ion replacement. This circumstance provides almost two-fold economy in the LWS ownership cost during a 20-year operation period, with a further increase in the economic profit. An additional advantage of using an LWS is a high level of localization of expenses (up to 85%), which creates opportunities for optimization of future capital expenditures for construction of such storage systems.

Figure 2. Cumulative total cost of ownership for an energy storage system with 200 MW of installed power and 800 MWh of energy capacity as a function of duration of the ownership period
Projects Overview
Startups Gravitricity and GravityPower (www.gravitricity.com; www.gravitypower.net) propose using abandoned mines for vertical weight movement, which is an innovative closed-cycle economy approach. To increase the total weight mass, Gravitricity's system uses additional weight in the upper-level storage area, as shown in Fig. 3. While this solution increases energy capacity of the storage system, it requires horizontal movement of weights, which in turn has a detrimental impact on both the efficiency and operational cost of the system. Seismic activities, a curvilinear path inside a mine shaft, groundwater, and wall maintenance are also major challenges to achieving positive economics for the project.
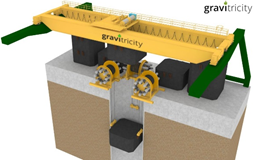
Figure 3. 3D model of the Gravitricity storage system. Source: www.gravitricity.com.
Energy Vault's storage system relies on the creation of an above-ground load-bearing structure with elevator shafts, as shown in Fig. 4. Unlike Gravitricity, where energy capacity relies on mine size, Energy Vault determines the number of lift shafts and weights based on the building footprint, offering greater scalability. According to the patent (Pedretti and Pedretti-Rodi, 2021), the weights move not only vertically but also horizontally to park the weights in a storehouse. The horizontal movement adversely affects efficiency and operational costs. The storehouse containing the weights being located away from the lift shafts significantly increases the area of the building, which increases the capital costs. In addition, high-rise cast-in-situ construction is affected by human factors and weather conditions which brings uncertainty into the terms of construction, and increases the cost as a result.
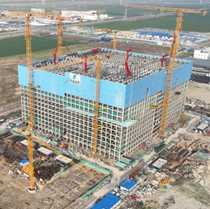
Figure 4. Photograph of the Energy Vault storage system in China. Source: www.energyvault.com.
The first concept developed by Energozapas company involved the horizontal movement of weights. The concept was tested using a lab-scale device in 2014 (https://youtu.be/he30p4qqNU4?si=cJFodfEruKOQkQxi), revealing low efficiency of the system. The second concept detailed in the patent (Soloboev and Bryzgalov, 2020) was developed in 2016, which is illustrated in the video (https://youtu.be/ec0j9eZa9Fw). This mechanism eliminates the horizontal movement of weights, resulting in increased efficiency and reduced operational costs. The storehouse is located directly above the shafts and thus it does not increase the building area, which considerably affects the capital cost. The second concept was successfully tested on a 20-meter-high energy cell in 2016 (https://youtu.be/NhGECJTvDrc). The industrial design of Energozapas is based on the utilization of a reinforced concrete skeleton enclosed by a cylindrical casing, providing protection against wind forces to reduce the amount of skeleton material, as seen in Fig. 5.
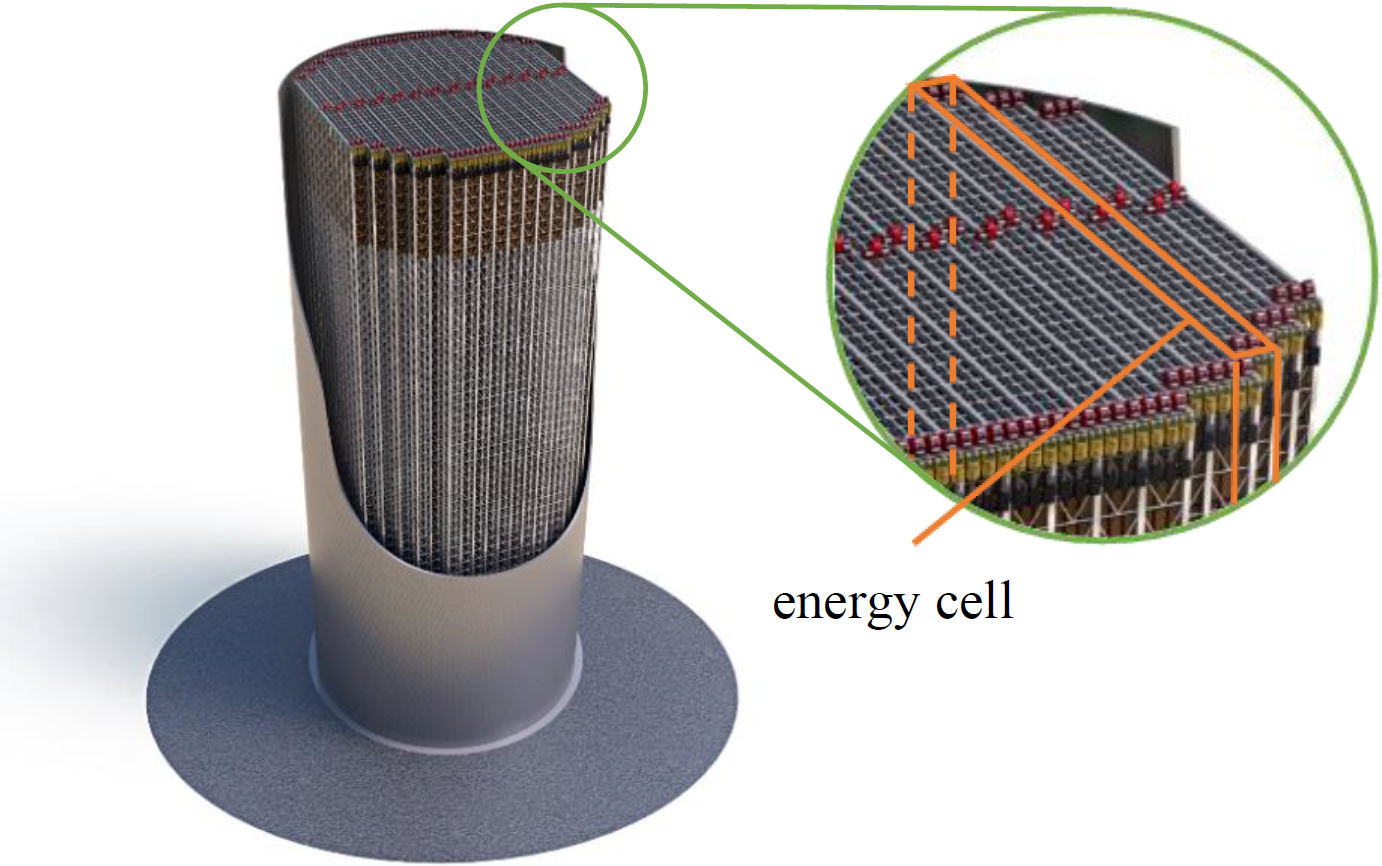
Figure 5. 3D model of the Energozapas storage system. Source: Energozapas LLC.
To make the most of the available space within the cylindrical shell, adjustments to the energy cell sizes are essential, as depicted in Fig. 5. Consequently, different cell sizes accommodate varying quantities of weights, leading to energy capacity varying from cell to cell. This complexity adds intricacy to the control of the storage system. Additionally, constructing a thin-walled reinforced concrete shell presents a technically demanding task. In 2021, Energozapas developed the technology of robotic construction for a reinforced concrete load-bearing skeleton of LWS (https://youtu.be/Vi0BYnK4CBM).
In 2023, GRAVIENT introduced a new gravity storage design (https://vimeo.com/885627271/b54b4becb4), as shown in Fig. 6. This design features a rectangular base, allowing for the installation of energy cells with consistent capacity. GRAVIENT's weights move only vertically and are constructed using unstabilized compressed earth blocks (uCEB) technology (Kropotin, Penkov, and Marchuk, 2023). These uCEB weights have a carbon footprint that is 7 times lower than that of concrete-based weights, and are at least 1.5 times more cost-effective (Kropotin, Penkov, and Marchuk, 2023). Both materials also facilitate the incorporation of industrial waste and artificial reinforcing fibers, which can be sourced from various outlets, including recycled wind turbine blades. Unlike all the other projects mentioned above, GRAVIENT chose to eschew the usage of a concrete-based load-bearing skeleton in favor of green steel. Steel is well-suited to handle seismic and wind loads. This shift is a pivotal step towards minimizing the carbon footprint.
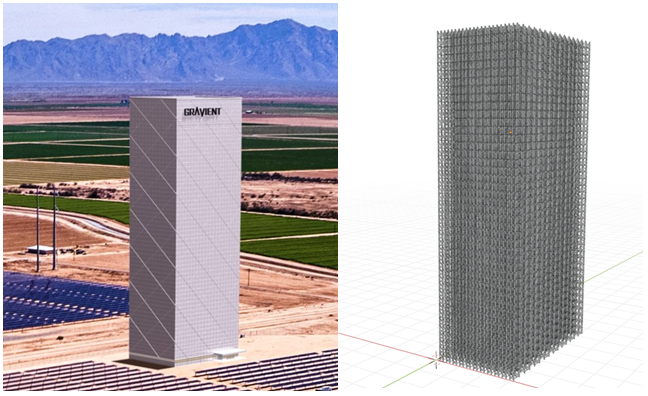
Figure 6. 3D model of the GRAVIENT storage system. Source: www.gravient.com.
GRAVIENT's energy storage project employs robotic assembly for its load-bearing skeleton. Robotic assembly can reduce construction costs and terms several times, especially in the case of high-rise buildings. While specific project details are currently limited, it can be inferred that the components of the steel load-bearing skeleton are lighter and more compact compared to equivalent reinforced concrete elements with similar load-bearing capacity. Consequently, the cost of robotic construction for the steel skeleton is lower than that for its reinforced concrete counterpart.
Conclusion
Today, there are sufficient experimental materials and models that confirm the high efficiency, low operating costs, long service life and even the high maneuverability within the millisecond range of lifted-weight storage (LWS). As a result, LWS can offer various services, including load shifting, renewable energy integration, black start capability, absorbance of reactive power, and even fast-response frequency regulation. These systems utilize readily available materials and components. Despite their considerable height, the construction is relatively straightforward, and the footprint is comparable to lithium-ion (Li-ion) batteries. Additionally, LWS is an absolutely safe, fireproof, and environmentally friendly solution that does not contain toxic elements. As a result, LWS is capable of providing at least the same services as Li-ion batteries and the revenue stream for LWS is no less than that of Li-ion storage.
On the other hand, there is a lack of studies regarding the capital cost estimation. It is worth noting that the total cost of ownership (TCO) estimation presented for LWS in Fig. 2 is based on the calculation of capital cost provided in the article by Kropotin and Marchuk (2023a). The authors emphasize that the capital cost value includes the costs of materials, labor, taxes, equipment, subcontractors, overheads as well as construction company profits. However, it does not take into account economies of scale. This is worth considering because the construction of a LWS facility requires large quantities of supplies, and a significant portion of these supplies can be sourced locally at the construction site. Furthermore, the calculation used by Kropotin and Marchuk (2023a) assumes an ordinary frame design of a high-rise building. It does not take into account construction design optimization or the implementation of robotic construction technology to reduce the capital cost of LWS. Consequently, it is anticipated that the actual ownership cost for LWS is significantly lower than that shown in Fig. 2. On the other side, the Li-ion curve in Fig. 2 is based on the data taken from the U.S. Department of Energy report and it can hardly be challenged downward, since it is the actual cost of such projects. So, even with the strong assumptions made in this comparison in favor of Li-ion storage, LWS shows a significant advantage demonstrated in Fig. 2.
In sum, the longer the ownership horizon we consider, the more advantageous the use of the LWS becomes. The long lifetime of LWS reduces the total cost of ownership. For example, if the lifetime of Li-ion storage is limited to 10 years, the cost of LWS ownership with a 50-year service life decreases by a factor of 5 assuming all other conditions are the same. This fact offers many opportunities for LWS development and creates the potential for positive future economic growth.
REFERENCES
Berrada, A., Loudiyi, K., and Zorkani, I. (2016) Sizing and economic analysis of gravity storage, J. Renew. Sustain. Energy, vol. 8(2): 024101.
Berrada, A., Loudiyi, K., and Zorkani, I. (2017) System design and economic performance of gravity energy storage, J. Cleaner Prod., vol. 156: 317–326.
Berrada, A. (2022) Financial and economic modeling of large-scale gravity energy storage system, Renewable Energy, vol. 192: 405–419.
Emrani, A., Berrada, A., Ameur, A. and Bakhouya, M. (2022) Assessment of the round-trip efficiency of gravity energy storage system: Analytical and numerical analysis of energy loss mechanisms, J. Energy Storage, vol. 55(A): 105504.
Franklin, M., Fraenkel, P., Yendell, C., Apps, R. (2022) Gravity energy storage systems, in Storing Energy, T.M. Letcher (Ed.), 2nd ed., Elsevier, 91–116.
Li, J., Wan, J., Xia, Y., Zhao, S., Song, G., and He Y. (2023) A feasibility study on gravity power generation technology by virtue of abandoned oil-gas wells in China, Energies, vol. 16(4): 1575.
Morstyn, T. and Botha, C.D. (2022) Gravitational energy storage with weights, in Encyclopedia of Energy Storage, L.F. Cabeza (Ed.), Oxford: Elsevier, 64–73.
Kropotin, P. and Marchuk, I. (2023a) Analytical and quantitative assessment of capital expenditures for construction of an aboveground suspended weight energy storage, Renewable Energy, 119587. https://doi.org/10.1016/j.renene.2023.119587
Kropotin, P. and Marchuk, I. (2023b) On efficiency of load-lifting rope-traction mechanisms used in gravity energy storage systems, J. Energy Storage, vol. 58: 106393.
Kropotin, P., Penkov, O., and Marchuk, I. (2023) On using unstabilized compressed earth blocks as suspended weights in gravity energy storages, J. Energy Storage, vol. 72: 108764.
Pedretti, A. and Pedretti-Rodi, M. (2021) Elevator Cage for Energy Storage and Delivery System, Energy Vault Inc., Patent No. US20210404445A1; 06/29/2021; 12/30/2021, US17/305,008 (US).
Soloboev, S.V. and Bryzgalov, A.A. (2020) Industrial System for Energy Storage, Energozapas LLC, Patent No. US10833533B2; 12/27/2018; 02/06/2020, US2020/0044481A1 (US).
Tong, W., Lu, Z., Zhao, H., Han, M., Zhao, G., and Hunt, J. D. (2023) The structure and control strategies of hybrid solid gravity energy storage system, J. Energy Storage, vol. 67: 107570.
Viswanathan, V., Mongird, K., Franks, R., Li, X., Sprenkle, V., and Baxter, R. (2022) Grid Energy Storage Technology Cost and Performance Assessment, U.S. Department of Energy.
参考文献
- Berrada, A., Loudiyi, K., and Zorkani, I. (2016) Sizing and economic analysis of gravity storage, J. Renew. Sustain. Energy, vol. 8(2): 024101.
- Berrada, A., Loudiyi, K., and Zorkani, I. (2017) System design and economic performance of gravity energy storage, J. Cleaner Prod., vol. 156: 317–326.
- Berrada, A. (2022) Financial and economic modeling of large-scale gravity energy storage system, Renewable Energy, vol. 192: 405–419.
- Emrani, A., Berrada, A., Ameur, A. and Bakhouya, M. (2022) Assessment of the round-trip efficiency of gravity energy storage system: Analytical and numerical analysis of energy loss mechanisms, J. Energy Storage, vol. 55(A): 105504.
- Franklin, M., Fraenkel, P., Yendell, C., Apps, R. (2022) Gravity energy storage systems, in Storing Energy, T.M. Letcher (Ed.), 2nd ed., Elsevier, 91–116.
- Li, J., Wan, J., Xia, Y., Zhao, S., Song, G., and He Y. (2023) A feasibility study on gravity power generation technology by virtue of abandoned oil-gas wells in China, Energies, vol. 16(4): 1575.
- Morstyn, T. and Botha, C.D. (2022) Gravitational energy storage with weights, in Encyclopedia of Energy Storage, L.F. Cabeza (Ed.), Oxford: Elsevier, 64–73.
- Kropotin, P. and Marchuk, I. (2023a) Analytical and quantitative assessment of capital expenditures for construction of an aboveground suspended weight energy storage, Renewable Energy, 119587. https://doi.org/10.1016/j.renene.2023.119587
- Kropotin, P. and Marchuk, I. (2023b) On efficiency of load-lifting rope-traction mechanisms used in gravity energy storage systems, J. Energy Storage, vol. 58: 106393.
- Kropotin, P., Penkov, O., and Marchuk, I. (2023) On using unstabilized compressed earth blocks as suspended weights in gravity energy storages, J. Energy Storage, vol. 72: 108764.
- Pedretti, A. and Pedretti-Rodi, M. (2021) Elevator Cage for Energy Storage and Delivery System, Energy Vault Inc., Patent No. US20210404445A1; 06/29/2021; 12/30/2021, US17/305,008 (US).
- Soloboev, S.V. and Bryzgalov, A.A. (2020) Industrial System for Energy Storage, Energozapas LLC, Patent No. US10833533B2; 12/27/2018; 02/06/2020, US2020/0044481A1 (US).
- Tong, W., Lu, Z., Zhao, H., Han, M., Zhao, G., and Hunt, J. D. (2023) The structure and control strategies of hybrid solid gravity energy storage system, J. Energy Storage, vol. 67: 107570.
- Viswanathan, V., Mongird, K., Franks, R., Li, X., Sprenkle, V., and Baxter, R. (2022) Grid Energy Storage Technology Cost and Performance Assessment, U.S. Department of Energy.